If you’re a facility manager, you’ve probably heard of planned maintenance. If you work at a hotel or manage apartments, you must already know how vital it is but might be wondering if it is necessary.
Well, maintenance is crucial and shouldn’t be ignored. Deferring it often leads to unplanned asset failures, which can sometimes be stressful and time-consuming to fix.
If your team still operates on a reactive approach to maintenance, it’s time for a change. A solid planned maintenance schedule is key to keeping your facility safe and operable. Having one in place will help keep your hotel or apartment running smoothly, increase overall guest satisfaction, reduce large expenditures, and ultimately save you more time.
It’s also essential for general safety, cleanliness and, in many cases, compliance with brand standards. Use this guide to planned maintenance as your one-stop shop for understanding and implementing a successful facility maintenance program.
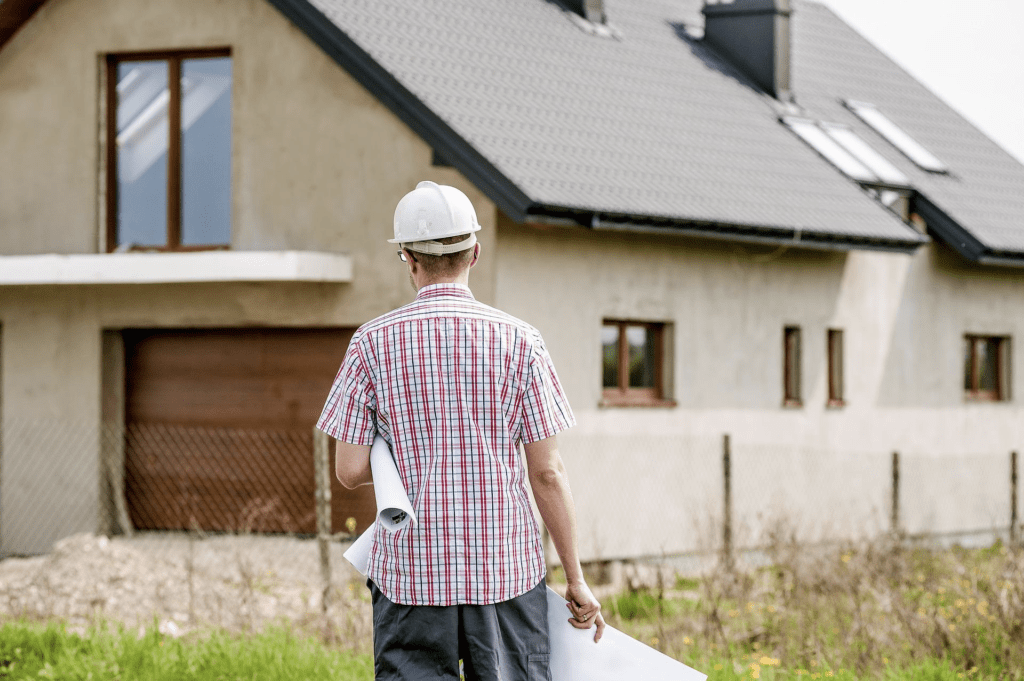
What Is Facility Maintenance?
Facility maintenance refers to the upkeep of various systems and components used in the facility. These systems often include general building operations such as degreasing surfaces and many needs specific to the facility and your customers. These particular needs are widely varied, and their scope usually depends on the size of your facility and the services you offer.
Planned facility maintenance may include restocking bare essentials like gloves for your maintenance staff, periodic soap replacements, and regularly changing bathroom mats. This broad scope of maintenance needs often requires extensive expertise from the maintenance crew.
It also means that maintenance planning is crucial for business success, especially with research findings that suggest 57 percent of delighted guests become repeat customers and 89 percent will recommend your brand.
Who Stands to Benefit More from Facility Maintenance?
Facility maintenance usually saves time and money in the long run, but it requires a time commitment to plan activities and define their scope. As a result, it often seems more complex at first, and there may be some resistance from staff members. However, the time invested in planning and scheduling is a small price to pay, considering all the resources that you’ll save by fixing problems before they happen
With that said, here are those who stand to benefit more from a planned maintenance schedule:
- Serviced Apartment Managers: Special residential units meant to offer longer stay times, and their maintenance needs resemble those of apartments rather than hotels. Even so, their maintenance needs are still quite varied.
- Hotel Managers: An average hotel needs a wide variety of maintenance work, including surface degreasing, plumbing, grounds keeping, lighting, bathroom supplies, and myriad others.
- Timeshare Rental Managers: Renters purchase accommodations for a certain period each year and are often responsible for funding some of the maintenance of the property.
- Resort Managers: Resorts located in remote locations have unique maintenance needs. Often, they need to supply their own electricity, water, and waste disposal, all while keeping up with the additional features they offer. Examples of extra features include golf courses, landfill sites, and swimming pools.
- Casino Hotel Managers: Casinos provide lodgings as a secondary function to their primary means of business. Those lodgings require just as much upkeep as other hotels. In addition, the machines, room, and food service areas on the property also require consistent maintenance work.
Insights on Creating and Implementing a Maintenance Schedule
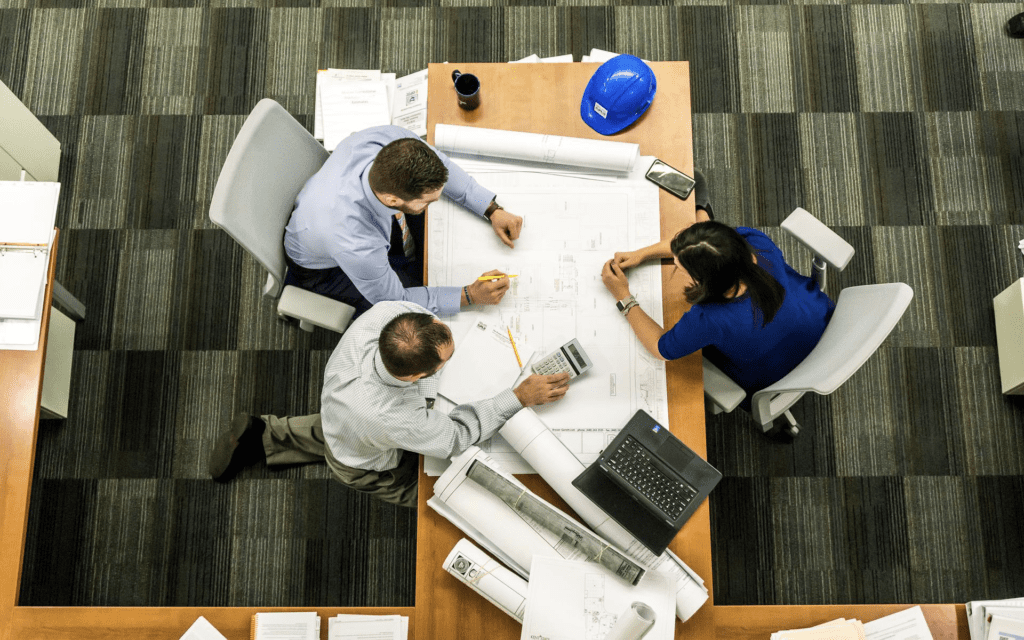
Sure, you can create and implement a planned maintenance schedule for your facility with sheer willpower. You can do it without changing anything in your project or management structure. However, the results that you will get will not be sustainable.
What you put in place will rely on a few strong individuals in the organization. As soon as some of them leave or move on to new roles, the maintenance planning process falls apart, and so does the scheduling process.
This means that you lose the most or even all of your gains, which is a waste of your efforts.
Without a structured approach, your implementation of planning and scheduling maintenance will fail eventually. In addition, without a focus on change management or engaging stakeholders, you will also fail.
Those that would have been on your side become blockers, ensuring that you are stuck due to resistance.
As a result, you might end up redoing everything or restarting the implementation process again. You don’t want to be doing that, as it’s complex and frustrating.
Whether big or small, adopting a structured approach is essential to the success of your organization. It will help to keep you on track. It will ensure you don’t skip essential steps during creation and implementation.
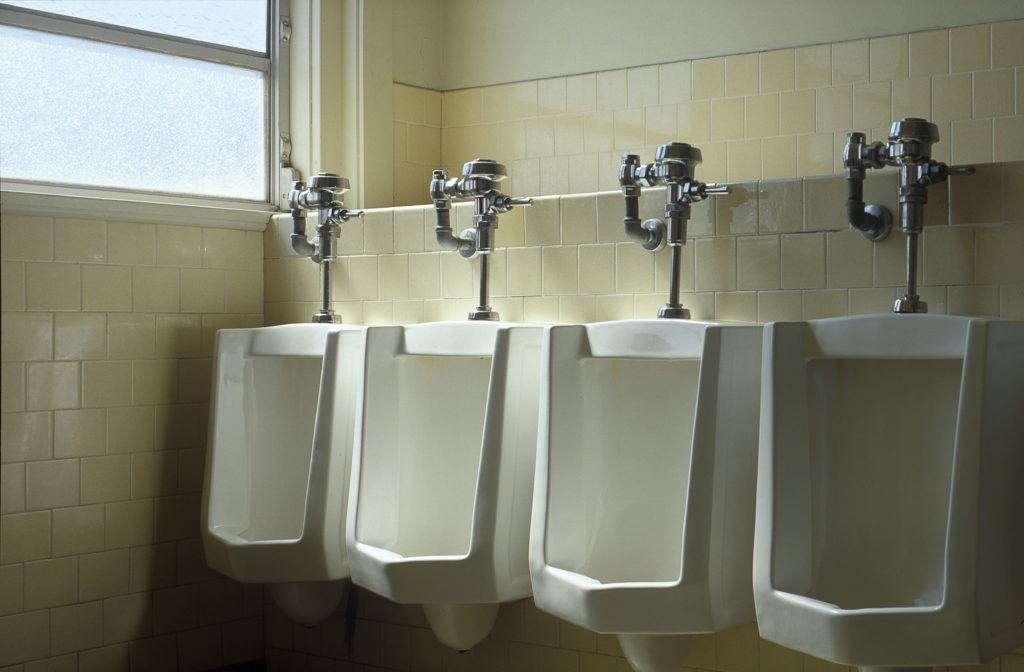
How Frequent Should Facility Maintenance Be?
Ideally, all maintenance processes often start with inspections. Inspections typically include all objective assessments (where you have to measure something) using a particular instrument for personal checks (where you only have to look, listen, feel, and smell).
To set frequencies, you will need to capitalize on the failure-developing period.
The failure-developing period (FDP), also known as the Pf Curve, refers to a specific period from when it is possible to detect a failure until we have a breakdown. Failure here refers to when a system seizes from operating correctly or when all necessary resources become depleted within given parameters, but it shows signs of problems.
For example, when your stock of multisurface degreasers drops below allowable amounts, but there is still enough to support maintenance operations. That’s a failure, and ignoring it might eventually become a complete breakdown, where a slight lack of the product will impede maintenance and, in turn, taint the business.
In general, FDP refers to the time difference between the failure and the breakdown. If the failure was noticed at 6 a.m. and the breakdown occurred at 6 p.m. four days later, the FDP will be 108 hours.
So, how frequent should I inspect my facility?
You will have to divide the FDP by two to get the inspection frequency. For instance, if your FDP is 14 days and you need some time to plan and schedule corrective maintenance, your inspection frequency should be seven days.
Keep in mind that if the inspection frequency is longer than the FDP, you are more likely to miss the failure and might run into trouble.
To be safe, some managers often plan to replace and renew items to restore their reliability at a fixed time regardless of their condition. These intervals often vary between weeks, months, bimonthly, or quarterly depending on how much traffic they receive.
What Makes a Maintenance Schedule Effective and How to Make One
An effective maintenance schedule needs to cover all the features of the relevant facility policy. It should contain an exhaustive inventory of assets that you need to maintain. So make sure that you don’t leave out any essential items.
You’ll also need to identify the specific maintenance tasks you intend to perform. Where possible, align these tasks to individual assets. A reasonable maintenance schedule should also suffice in guiding the whole maintenance program.
For efficient maintenance of assets, you will need to demonstrate the skills-set required for each maintenance task. You don’t want to hire an inadequately skilled individual to handle the maintenance. The different levels of maintenance will guide you as you prepare this section.
To create one, you will need to know how long specific items in your facility tend to last. While this method tends to make planned maintenance relatively easy, you may risk doing it too often, especially if you will not factor in traffic and usage.
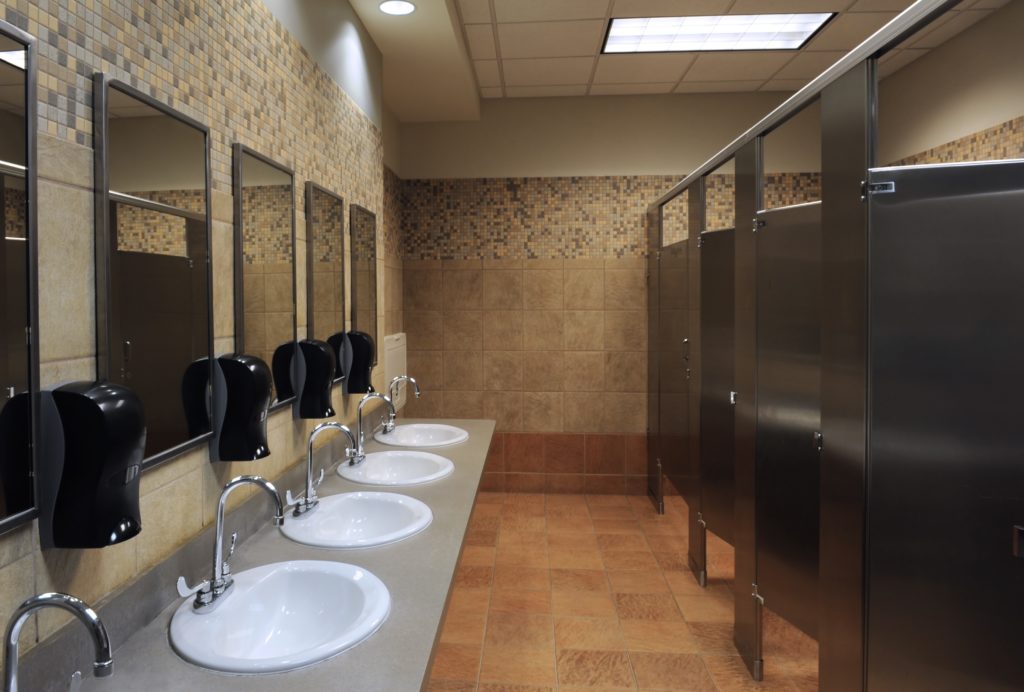
As a rule of thumb, always apply this strategy to short-life-assets such as bathroom tissues and paper towels. A good example is constantly checking and inspecting such bathroom assets every week.
You can use a digital maintenance management system to automate the process and create, plan, and execute a calendar-based maintenance schedule. This typically gives a simplified maintenance task overview based on the available item list.
With only a few clicks, you can activate, finish, print, and follow the status of each maintenance task. You can also see technical information like work orders and change details in your plan, automatically creating new due dates.
Moreover, you will also get an overview of the inventory and maintenance history to help reduce downtime.
The True Impact of Facility Maintenance
Facility maintenance is any maintenance activity that is planned and scheduled, aiming to reduce downtime by ensuring that all necessary resources are on hands—such as labor and parts, and a strategy for their usage. It is a helpful tool for making maintenance operations more efficient. It guarantees that you’ll always have the right strategy and resources to tackle any kind of maintenance quickly and easily, whether scheduled or not.
Although implementation will differ from one facility to another, some successful ways to organize assets, automate your maintenance schedule, train your team on proper execution, and abide by your maintenance checklists. With all these tools and methods, your team will spend less time putting out fires and more time looking for improvement opportunities.